How to Choose the Best Quality Inspection Software? (+ Top Picks)
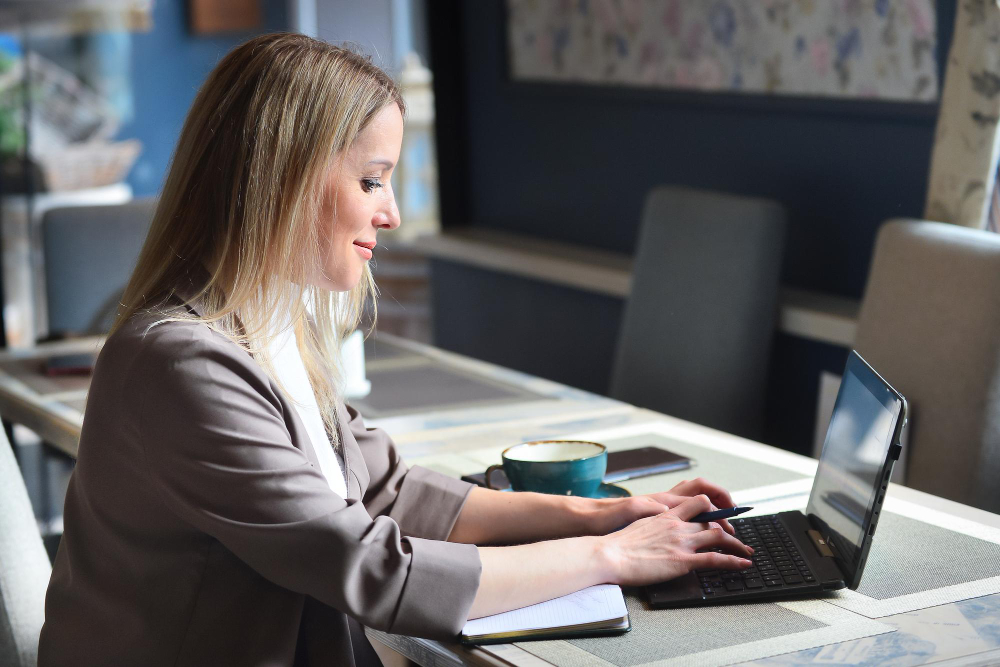
Take Control of QA.
Make Inspections Effortless.
We’ll quickly uncover your needs and share how we can help—no pressure, no stress, just solutions. Grab your spot on our calendar today!
Do you find it hard to keep high-quality standards? Choosing the best quality inspection software can make a huge difference.
Businesses can transform quality control processes, save money, and guarantee product excellence with the right software solution.
In this guide, we'll teach you how to choose the best quality control software. We'll also cover the top solutions you can consider.
But first, let's discuss the importance of quality inspections and common challenges you may face.
The Importance of Quality Inspections
Quality inspections are vital for any business that aims to deliver top-notch products or services. They help you meet regulatory requirements and guarantee safety.
Consistent quality inspections also allow you to catch quality issues early. No need for costly reworks or recalls later on. Plus, you can protect your brand's reputation.
When your products meet high standards, your customers are also more likely to be satisfied. And happy customers tend to be repeat buyers. They can even recommend your brand to other people.
Common Challenges in Traditional Quality Inspection Processes
Businesses face many challenges when using traditional quality inspection processes. These challenges can hinder your efforts to maintain high product quality and meet customer satisfaction.
Let's take a closer look at each one below:
Human Error and Inconsistency
One of the biggest issues with traditional quality inspection processes is human error.
Manual inspections rely heavily on individual judgment, which can vary from person to person. Missed defects or false positives can result from this.
For example, if an inspector is tired or distracted, they might overlook a critical flaw in a product during visual inspection.
Over time, these errors can add up. Your product quality and customer satisfaction are negatively affected.
Time-Consuming and Labor-Intensive
The traditional inspection process is often time-consuming and labor-intensive. Imagine checking each product or service manually.
This can slow down your manufacturing operations. Delays and increased labor costs can arise from this.
Difficulty in Tracking and Documentation
Traditional methods often involve paper-based records. Staff members can easily lose or damage quality assurance (QA) documents. Even if you use spreadsheets, manual data entry can be prone to errors.
This is why many businesses find it difficult to track inspection results and maintain accurate documentation.
Limited Data and Insights
Manual inspections provide limited data and insights. You'll find it hard to analyze inspection results and identify patterns in quality issues.
For example, you might not notice that defects are more common during certain shifts or at specific production stages. Because of this lack of data, you can't make informed decisions to address this problem.
Poor Communication and Coordination
Traditional quality inspection methods can suffer from poor communication and coordination. The quality control team, production staff, and management must be on the same page to ensure smooth operations.
However, without centralized systems, employees often lose or forget important information. Expect more mistakes and production inefficiencies because of this.
Compliance and Regulatory Issues
If you're in a highly regulated industry, you know that meeting compliance and regulatory requirements is crucial.
Unfortunately, traditional inspection methods make it hard to know if products meet quality standards.
For example, if records are incomplete or inaccurate, you can't easily ensure compliance. You may end up paying costly fines or facing legal issues.
Benefits of Implementing Quality Inspection Software
After knowing the challenges of traditional quality inspections, you now understand the need for a better solution. This is where quality inspection software comes into play.
It can offer numerous benefits to your business:
Increased Accuracy and Consistency
One of the biggest advantages of using quality inspection software is the significant increase in accuracy and consistency.
Automated inspection systems reduce the risk of human error. They inspect every product or service by following the same inspection criteria. They can also catch issues that manual inspections usually overlook.
Due to these advantages, you can maintain product quality and boost customer satisfaction.
Enhanced Productivity and Efficiency
Quality control software improves operational efficiency. It can handle large volumes of products much quicker than manual methods.
Automated workflows can also reduce bottlenecks in your production line. You can easily meet deadlines and increase your team's productivity.
Better Decision-Making
Quality inspection software provides valuable data and analytics.
With real-time insights, you can quickly identify trends and patterns that were previously hard to see. This promotes a proactive approach to quality inspections.
You can also take immediate corrective action to improve manufacturing processes.
Improved Compliance Management
Using quality inspection software can track compliance with industry standards. It keeps detailed records of all inspections. This makes it easier to prove adherence to state and federal regulations during audits.
The quality management system also provides automated alerts. Once you get notified of any potential issues, you can address them before they become bigger problems.
Cost Savings
Investing in quality inspection software can lead to significant cost savings. Since it identifies problems early, you cut costs related to returns, repairs, and recalls.
Additionally, it allows your team to do more with fewer resources. You no longer need to hire additional staff for quality assurance and inspections. You can allocate resources more effectively with automated systems.
How to Choose the Right Quality Inspection Software for Your Business?
If you want to enjoy all the benefits of quality inspection software, you should select the right solution.
Follow the steps below to make the best choice.
1. Understand Your Business Needs
Start by understanding your specific needs.
What are the biggest pain points in your current quality inspection process? Do you struggle with accuracy, speed, or compliance?
You should also ask yourself what you want to achieve with the tool. Is it to save time or improve document control?
Once you know your priorities, you can choose the right quality management software. For example, if you have a large volume of products for inspection, you want a solution that can scale with your growth.
2. Evaluate Software Features
The next step is to look for features that align with your needs. Here are some must-have capabilities:
- Real-time data collection: Choose a quality control software that offers actionable insights and real-time defect detection.
- Automated workflows: They speed up quality control processes while minimizing human errors.
- Reports and analytics: Use a tool that provides valuable data for continuous improvement.
- Mobile-friendly: Select a mobile inspection software that allows you to schedule and conduct audits from any location.
- Simple interface: Choose a user-friendly tool to conduct quality inspections without the hassle.
- Compliance management: It offers tools that ensure your products or services adhere to industry standards.
- Customization: The software you choose shouldn't be one-size-fits-all. It must allow customization to match your unique needs and objectives.
3. Research Vendor Reputation
Now that you know which features to consider, you should choose a reputable vendor.
Look for companies with a proven track record in your industry. Check their experience and case studies to gauge their reliability.
For example, if you own multiple restaurants, it's better to select a food safety management software solution. You can rely on the vendor to meet strict food and kitchen quality standards.
However, if you manage a senior home, choose a platform that helps you achieve senior living regulatory compliance.
4. Check Customer Reviews
You should also look beyond case studies and vendor expertise.
Consider customer reviews to learn how the quality management system performs. Look for feedback that mentions reliability, ease of use, customer support, and user satisfaction.
You should also pay attention to both positive and negative feedback to get a balanced view.
Use platforms like Capterra, G2, Software Advice, and Google to research customer reviews.
5. Consider Budget and Return on Investment (ROI)
It's important to choose a quality inspection system that fits your budget.
See past the initial price tag. Consider ongoing costs related to training and maintenance, for example.
You should also evaluate the ROI of digital audits you get from each tool. Will it lead to significant savings by ensuring product quality and reducing defects?
You can request detailed price plans from each vendor. Then, compare the costs and long-term benefits of different solutions.
6. Verify Software Scalability
Having feature-packed and affordable software is useless if it doesn't grow with your business.
Always think ahead and choose a scalable solution. Your operations will likely expand, so you need a tool that can handle increased volumes and larger teams.
7. Assess Security and Compliance
Your operations regularly deal with sensitive inspection data.
It's important to choose a software solution with robust security measures. It protects sensitive information while ensuring compliance with regulatory standards.
Best Quality Inspection Software Solutions
With so many platforms available, it can be overwhelming to select the right one for your needs. This is why we've done the research for you and listed the best inspection software solutions you can consider:
MyFieldAudits
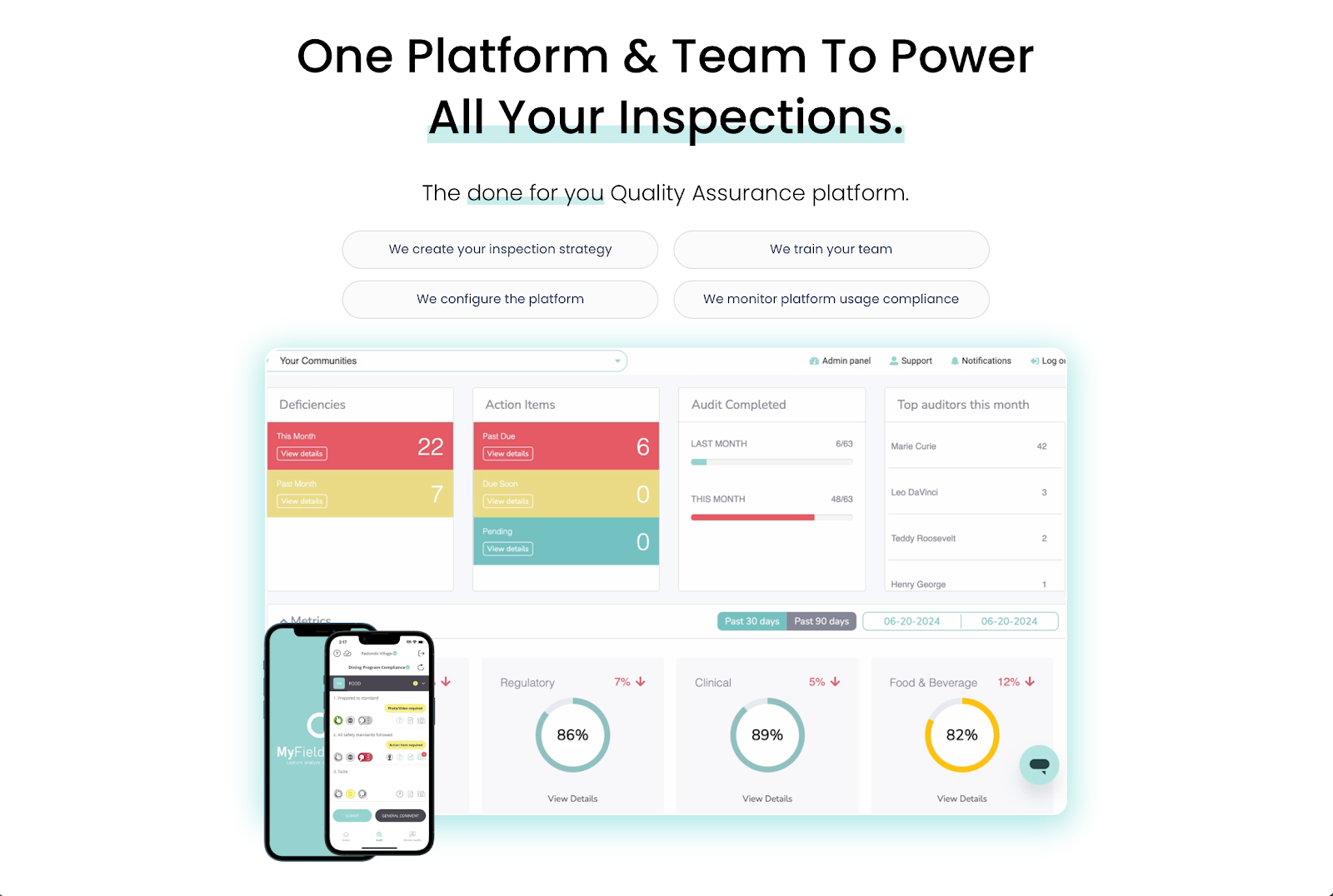
MyFieldAudits goes beyond traditional inspection software. It provides an enterprise-level solution tailored to large organizations that require advanced quality assurance and compliance tracking.
Unlike generic "do-it-yourself" platforms, MyFieldAudits partners with businesses to develop customized inspection workflows that meet industry-specific needs.
They can also configure the inspection app and provide employee training. This enables clients to focus on capturing valuable data for continuous improvement and company growth.
Book a discovery call today! Or watch this product overview video to learn how MyFieldAudits can benefit your organization.
Ideagen
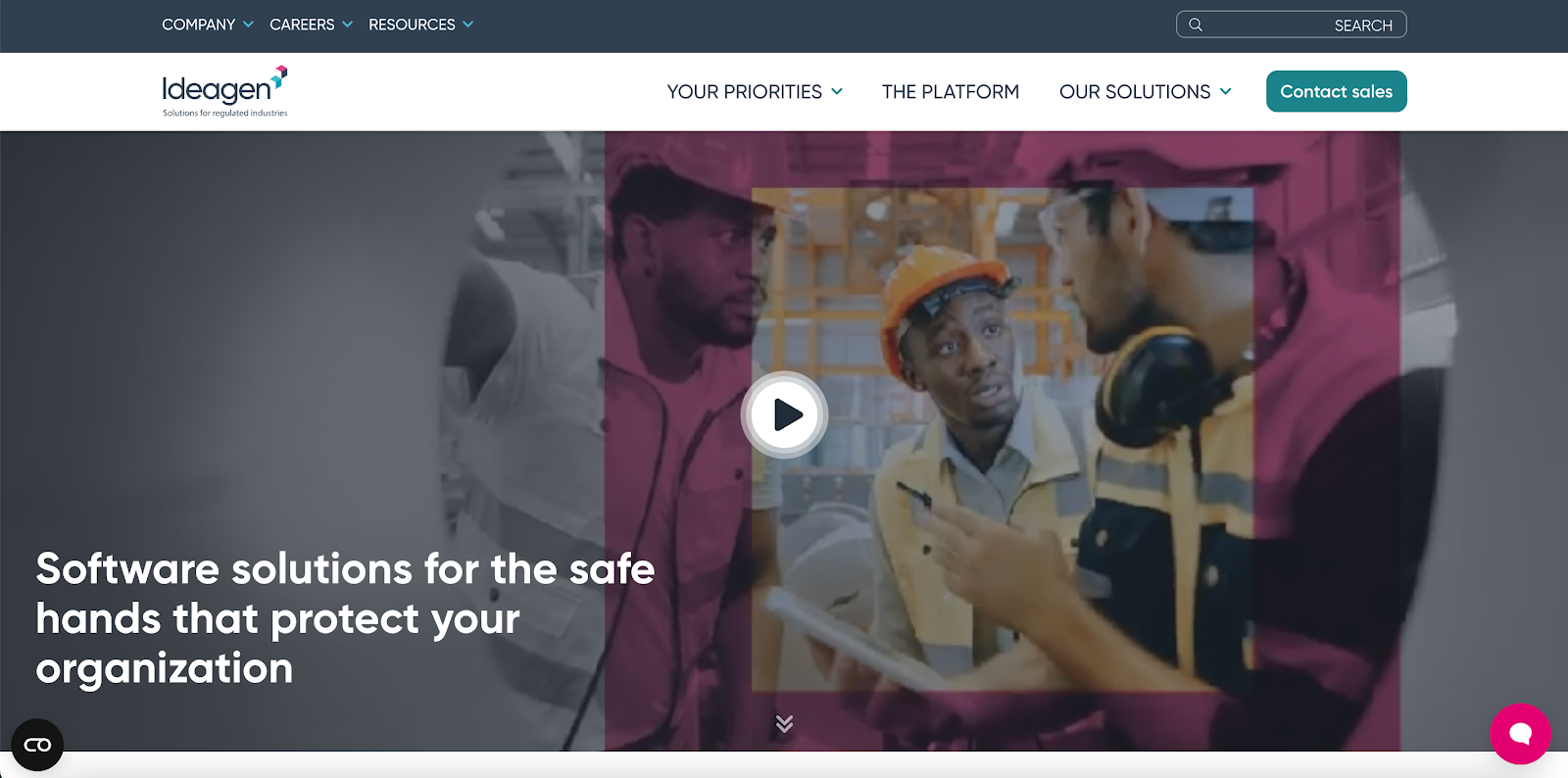
Ideagen offers a smart quality control software solution designed to automate inspections and documentation processes. It enables businesses to create reports up to 75% faster, which can reduce human errors and improve compliance.
Ideagen also features auto ballooning, OCR technology for data extraction, and customizable templates for inspection plans.
Plus, it supports various standards, including AS9102 FAI and PPAP, for traceable and compliant product development.
GoAudits
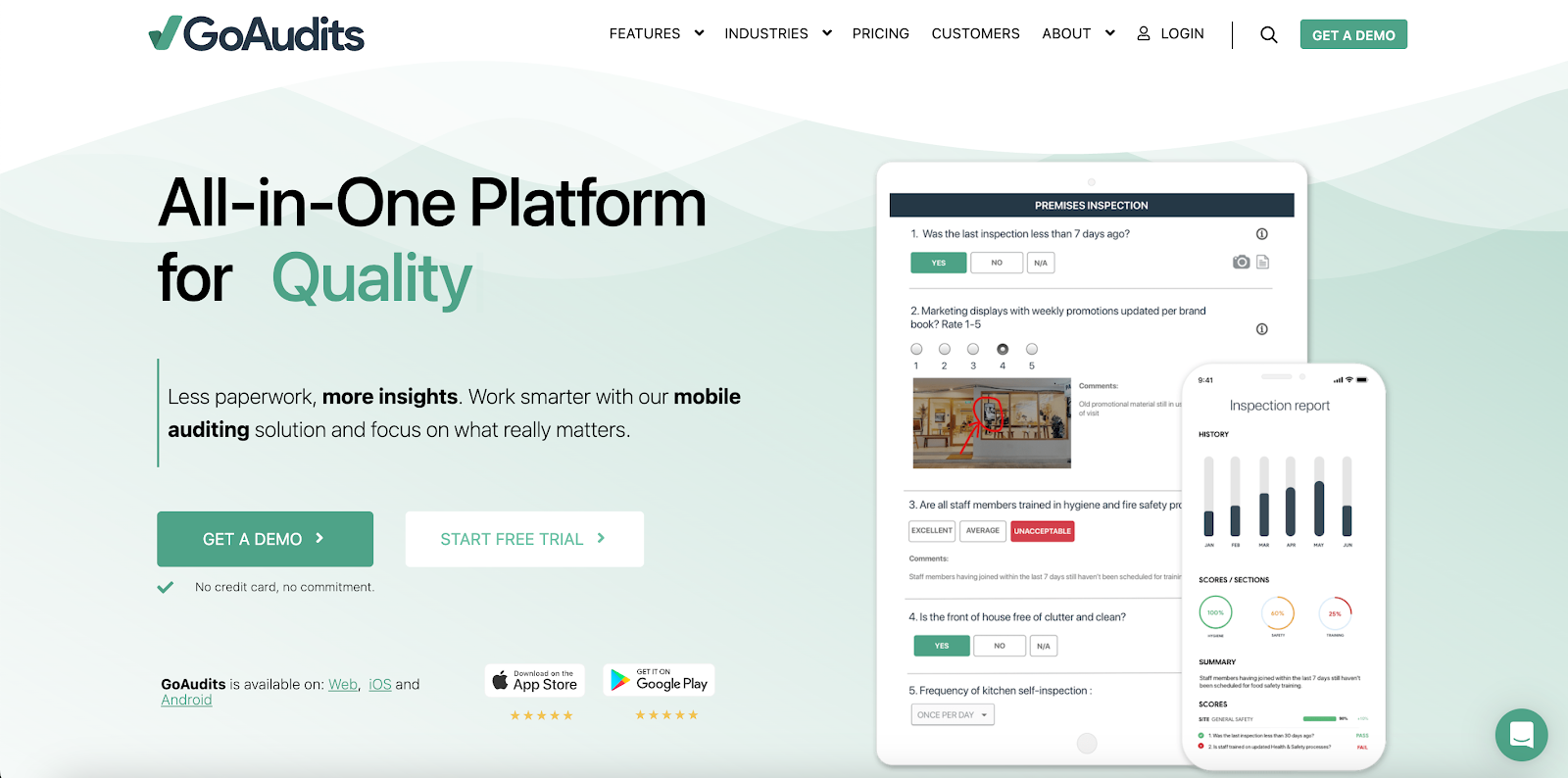
GoAudits is an all-in-one mobile auditing and inspection platform that simplifies quality assurance across various industries.
It enables QA professionals to conduct efficient inspections using custom digital checklists. The platform also incorporates photos, annotations, and e-signatures for increased visibility into operations.
Additionally, GoAudits offers real-time dashboards to monitor performance trends, assign corrective actions, and set up custom workflows. These enhance collaboration between frontline teams and management.
Lumiform
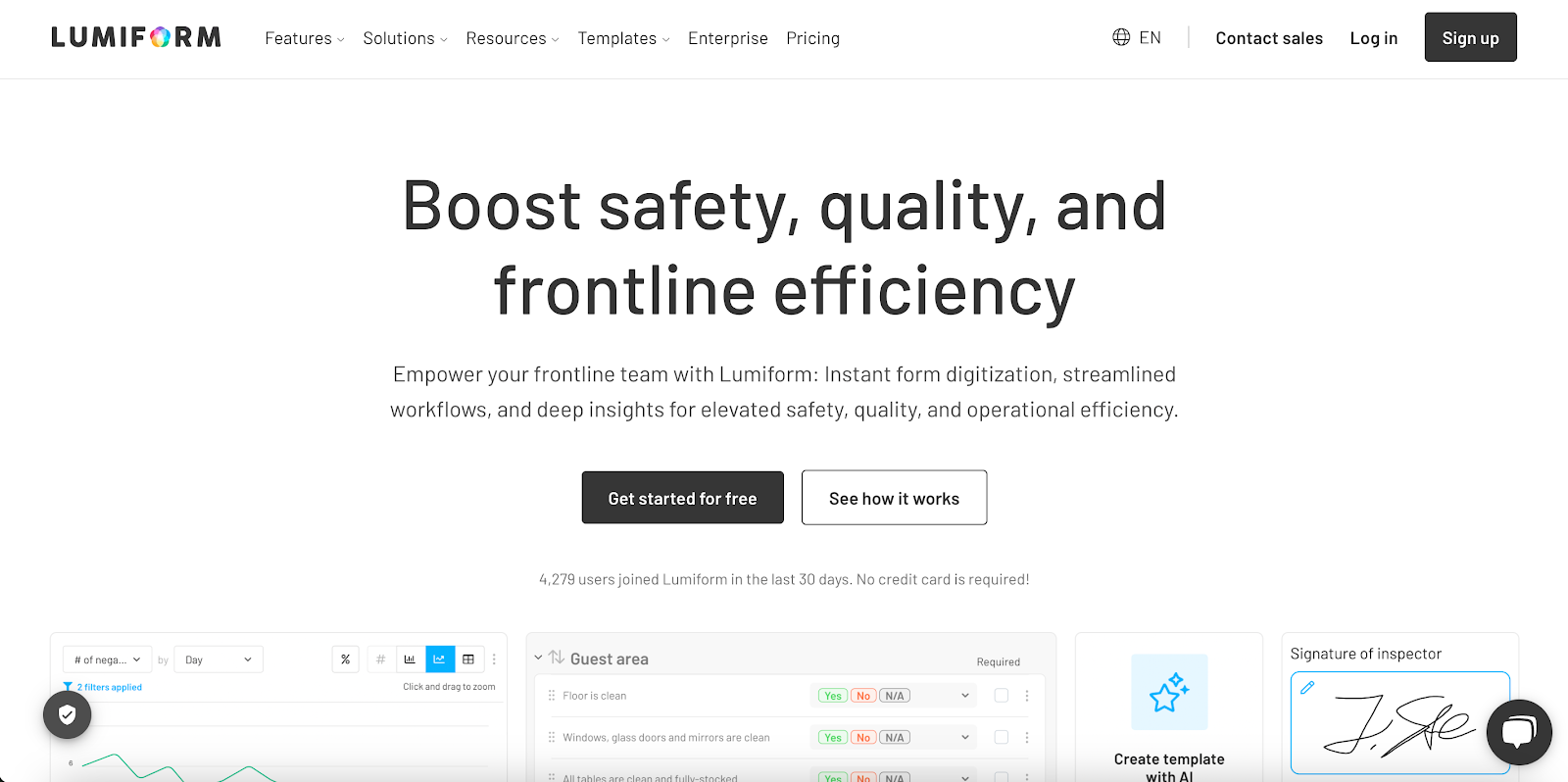
Lumiform can improve quality, frontline safety, and efficiency by digitizing and automating mobile forms. It has a library of ready-made templates that operators can use for quality inspections.
Lumiform also includes an intuitive form builder, which allows users to create custom digital checklists.
Plus, the platform can automate workflows to reduce manual oversight, eliminate routine tasks, and standardize operations.
ComplianceQuest
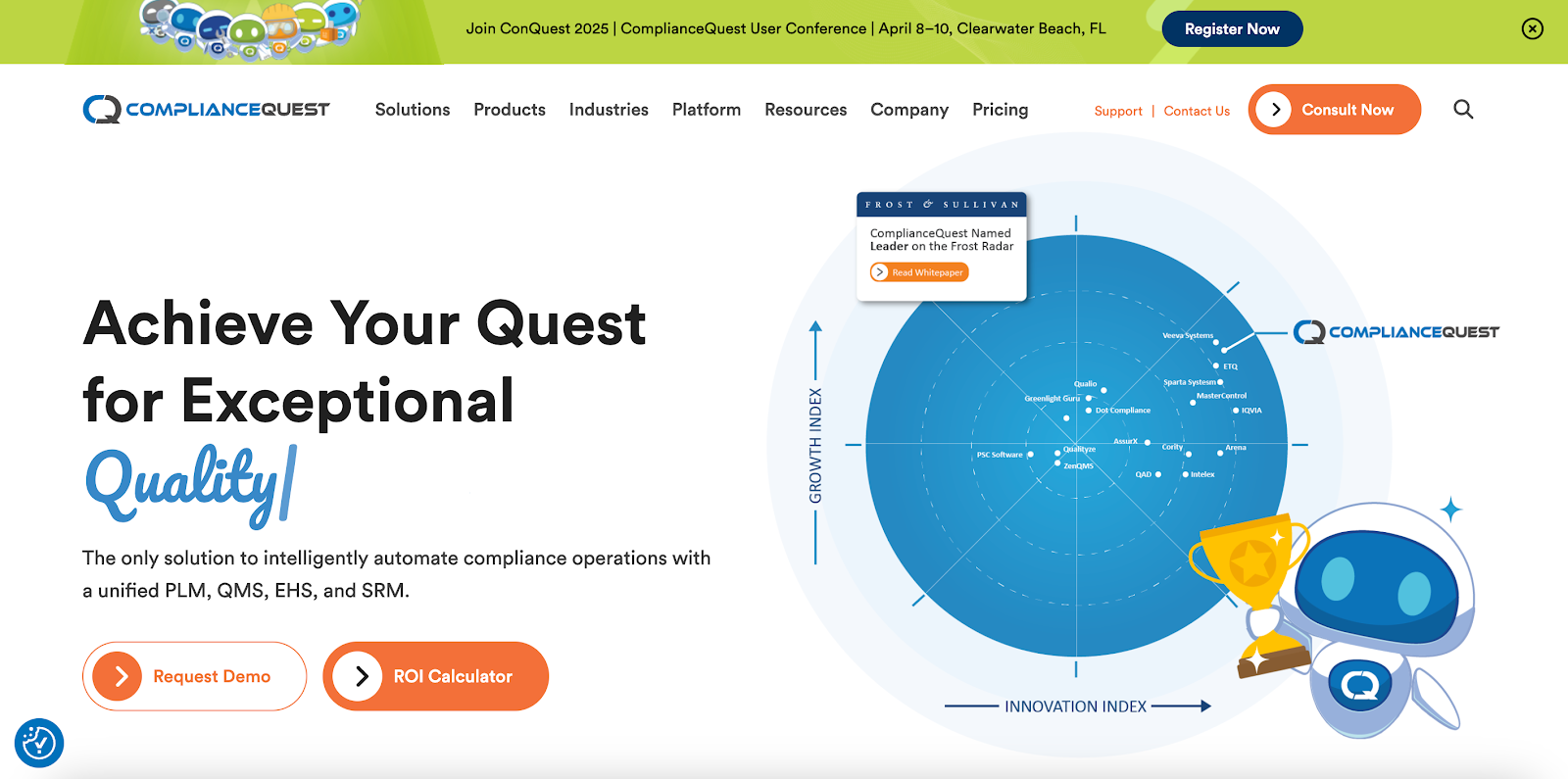
ComplianceQuest is a cloud-based quality management software for improving compliance, quality, and collaboration across supply chains.
It provides an extensive suite of solutions, including document control, audit management, risk assessment, and supplier quality management.
The platform also offers a user-friendly and secure system that integrates seamlessly with existing workflows.
How to Implement Quality Inspection Software Solutions?
After selecting the right quality inspection software, it's time to focus on implementing it. Below is a simple guide to help get the new system up and running.
Plan and Prepare
The first step is to plan the implementation.
You should define project goals and objectives. Think of what you need to achieve at each stage of the implementation process.
Then, you can set a realistic timeline to keep everyone on the same track.
Select the Right Team
After planning, choose a dedicated team to oversee the implementation. Include members from different departments who will use the software. Key participants should involve quality control, IT, and production staff.
You can consider all perspectives when you have a diverse team for the implementation. Plus, you increase the chances of meeting the needs of all users.
Migrate and Integrate Data
With the right plan and team in place, you can start migrating existing data.
You can integrate the new software with your current systems, like enterprise resource planning (ERP) and digital survey tools. Follow the integration instructions of the vendors.
After connecting both systems, check if data is transferred accurately. You must work closely with your IT team or the software vendor to solve technical challenges.
Customize the Software to Your Needs
Once the data transfer is complete, you can customize the software to match specific inspection processes and requirements.
You can set up custom compliance audit checklists, workflows, and reporting formats.
By adapting the tool to your needs, you can expect better quality inspections and promote data-driven decision-making.
Train and Onboard Users
Personalization is not enough. You should also train your team members so that they can use the new system effectively.
Provide comprehensive training sessions and resources. Then, combine hands-on training, online tutorials, and user manuals to accommodate different learning styles.
Pilot Test and Gather Feedback
Before full deployment, it's important to run a pilot test. Choose a small segment of your production line or a single department to use the software first.
Next, you can collect feedback from users and find any issues that may impact quality assurance.
Armed with this information, you can quickly address problems as needed.
Deploy the Quality Inspection Software
Once the pilot test is successful, you can proceed with full deployment.
Verify if all departments are ready and aligned. Additionally, check if all issues are resolved during the pilot phase.
Remember to monitor the early stages of full deployment. Even after careful planning and testing, problems can still arise. Solve them immediately to prevent future issues in quality assurance.
Successful Quality Inspections with MyFieldAudits
MyFieldAudits is a digital audit inspection solution designed for enterprise organizations in senior living, contract food service, and government sectors.
MyFieldAudits helps clients conduct thorough quality inspections with ease. They track compliance, monitor performance, and deliver actionable insights that drive continuous improvements.
Unlike other solutions that only provide access to a software app, MyFieldAudits handles everything from creating an inspection program to configuring the platform.
They can even train employees, which allows enterprises to focus on capturing the critical data that drives operational excellence.
Schedule a demo and get started today! Or watch this video to learn more about MyFieldAudits.
FAQs About Quality Inspection Software
How does quality inspection software improve business processes?
Quality inspection software improves processes through automation. It reduces errors and increases efficiency. The software also provides real-time data and analytics, so you can make better decisions. Plus, it offers other benefits, like improved product or cleaning quality, enhanced compliance, and increased cost savings.
What are the key features to look for in quality inspection software?
Consider features like real-time data collection, automated inspections, and reporting when choosing quality inspection software. Mobile access and compliance management are also important. These features provide accurate and efficient inspections that meet industry standards.
Can quality inspection software integrate with existing systems?
Yes, quality inspection software can integrate with other software like ERP (enterprise resource planning) and MES (manufacturing execution system). Thanks to this integration, you can ensure seamless data flow. It eliminates the need for manual data entry while reducing inaccuracies and human errors.